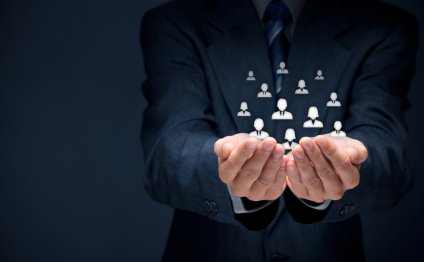
Progressive Healthcare Provider
About Progressive Healthcare
Progressive Healthcare is a large multi-specialty team practice with more than 100 main attention physicians and about 50 professionals. Progressive has 1, 600 employees and lots of places throughout a sizable south U.S. city.
We setup a two-day worth flow mapping occasion for them to prepare the modifications they want to make. It really is being held in just one of their particular large major treatment facilities. In the first day of the occasion, the summit area environment is one of span, doubt, and hope.
The attendees would be the senior managers (clinical and nonclinical) of the practice including marketing, two customers from an individual consultative team, and representatives from main attention management from different Progressive facilities.
It is necessary that stakeholders be represented so that they have actually a voice when you look at the results of the big event. We focus on a very brief introduction about lean reasoning additionally the types of waste in medical care.
FOCUS IS FROM THE PATIENT TECHNIQUES
The range of value flow modern desires to run is from the time someone needs a consultation for major attention until they show up in for it and leave the center.We have all a pad of paper and a pencil. We head out as an organization and go the worthiness flow.
We start in arranging
We check with the schedulers that which we do and that we are studying the workflow, not at people—we you will need to help people be comfortable about becoming observed by united states.
Lean Thinking Definition and Background
Lean reasoning is an activity to create price from the
customers’ viewpoint. Lean additionally targets
removing waste from work (procedures) that's
performed by every person after all amounts in the
business. Lean thinking originated by Ohno
in Toyota manufacturing range. Ohno regarded
waste as muda. He identified seven forms of waste in
manufacturing:
• Overproduction.
• Correction.
• information and information activity.
• Processing.
• Stock.
• Waiting.
• Motion.
Lean has been utilized thoroughly into the automotive
business. However, it is new to service and wellness
attention industries. General Motors, through a supplier
development system, shows its medical care
providers how-to do slim thinking activities. The
Institute for medical enhancement promotes lean
thinking with its enhancement collaboratives and
seminars. Lean reasoning is a manufacturing device
that centers around including worth from a patient point of
view and the removal of waste from processes/workflows.
We observe for 15-20 moments just how scheduling works and also make notes from the muda or waste we observe. It requires between three and seven moments to take a phone call after which set up a consultation.
Before we leave, we make inquiries of schedulers by what we've seen as well as their particular a few ideas for improvement. Mary Wecandoit, R.N., supervisor for this center, informs the value flow team it requires on average 10 days for an individual to see your physician.
They are data we use whenever we make our value flow map.
Then the group moves to the waiting area. Each person employs one or more client through the process. Visits differ in length. Therefore, we agree totally that we are going to follow customers from time they enter the door until they leave the facility for about 90 moments.
When each person is following a patient these are generally timing once the patient waits, timing how long it will take to do each one of the actions in go to process, plus noting the waste these are typically seeing.
Lean Design Principles
Worth
Value is really what an individual is willing to pay for. Exactly What
adds price from a patient’s perspective?
Value stream
a price flow may be the circulation of a certain solution from
a patient’s point of view. The scope of a value
stream can be defined during the process level, facility
level, organization-wide, or across numerous providers
within the continuum of take care of an individual.
Flow
Ignoring useful boundaries of work (or silos)
just how can care distribution be achieved without client
waiting and without interruption?
Pull
Pull is performing work as its requested or needed by a
step up a price flow. A push system does work
irrespective of whether or not the next move requires the
work done or if perhaps it really is prepared to get the solution or
item of the previous step/work.
Perfection
Excellence is striving for progressive elimination of
waste and implementing radical redesign of
procedures to incorporate value from someone point of
view. Excellence normally taking waste out from the treatment
distribution flow.
Perfection is generating transparency therefore
that all stakeholders can see just how a value stream is
performance. Excellence can also be contending against a
sight of brilliance, maybe not a rival.
Types of waste in health care:
• Handoffs (separates understanding, duty,
and action).
• Mistakes.
• Waiting.
• Barriers to communication.
• Information not available.
• Wrong information.
• Wrong device or no appropriate tool.
• Go see.
• Correction/rework/ evaluation.
• Inefficient motion.
• Material and information action.
• Policies and procedures maybe not employee/customer
focused or not flexible.
• Overproduction (a lot of, too fast, batches,
etc.).
People inside price flow team tend to be sharing what they are seeing that they wait for patients. Its interesting listening to all of them. Each is witnessing it through new eyes— as waste:
- “Look at how long they have to wait inside exam room.”
- “Never saw that before which is routine.”
- “What makes they doing that once more?”
- “We ask clients the same thing exactly how many times?”
- “Patients have to check-in again on lab?”
We gather inside summit area. We identify the main tips in the worth supply and compose all of them on flip charts. We agree that this is certainly Progressive’s current state value stream. Then everyone else begins writing examples of waste and nonvalue-added things they noticed.
Soon there clearly was writing surrounding each step of the process. Everyone steps returning to look at the whole value supply.
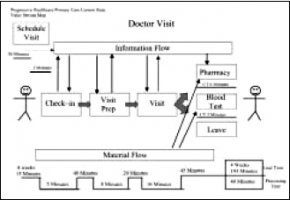
We ask ourselves how do we design a better future value flow? We start applying the design principles. We search for nonvalue-added observations.
The team takes a detour. Understanding value added? An individual may not be prepared to purchase waiting. Would they be happy to wait to ensure an allergy shot doesn't trigger them problematic? The team believes they should.
Share this Post
Related posts
Essence Healthcare Providers
When Healthcare is a “Lemon”: Asymmetric Information and Market
Read MoreSpanish for Healthcare Provider
We created a specialized language understanding platform, using you, the professional, under consideration. MySpanishTeacher…
Read More